Critical minerals are in the U.S., not in far-off mines
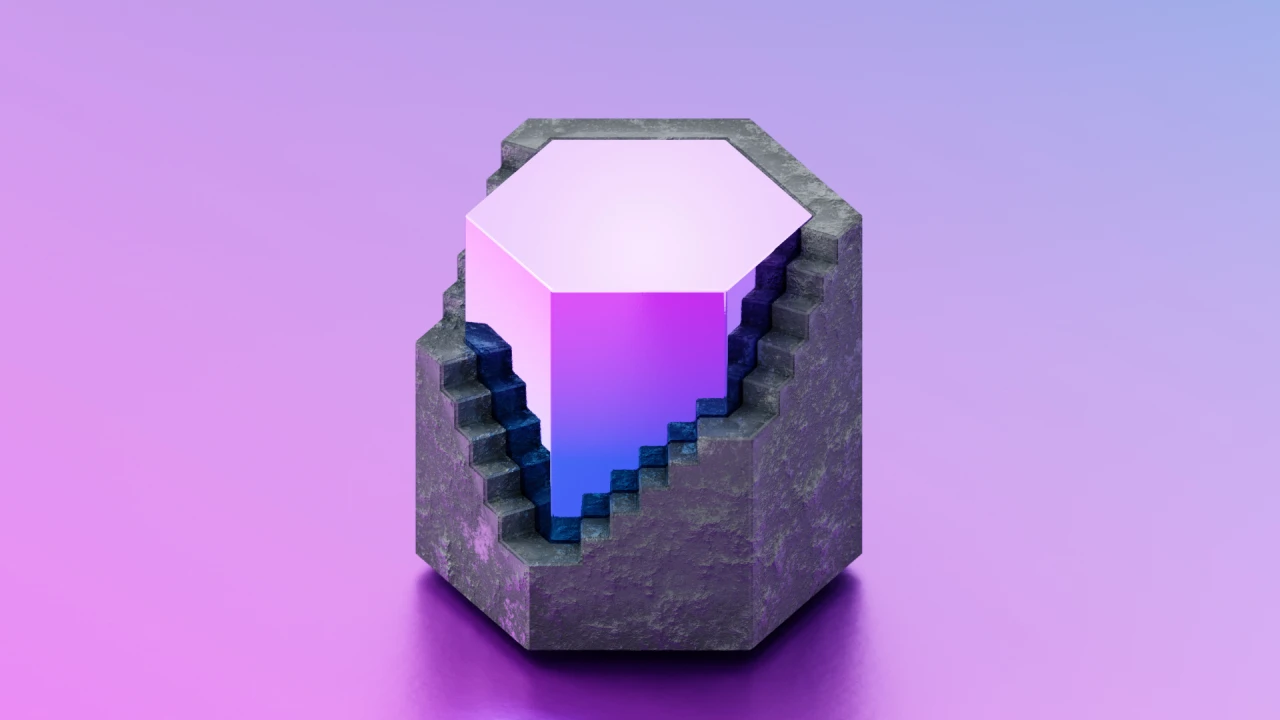
The clean energy transition is accelerating—but it’s running into a critical roadblock: the mineral supply chain. Lithium, cobalt, and other critical minerals power everything from electric vehicles to grid-scale batteries. But the world cannot mine these minerals fast enough to keep up.
By 2040, global demand for lithium alone is expected to surge more than 700%. Yet traditional mining remains slow, polluting, and geopolitically risky. Industry leaders and policymakers agree: We can’t build a sustainable tomorrow on an unsustainable supply chain.
But there’s a smarter solution—and it’s already flowing beneath us.
The minerals hidden in our water
Lithium and other critical minerals are already present in surprising abundance—not only in traditional hard rock or salar basins, but in often-overlooked water sources like geothermal brines, industrial effluents, and oilfield produced water. For years, these streams were dismissed as too complex or costly to process. But that’s beginning to change.
Advancements in direct lithium extraction (DLE) are now making it possible to recover lithium from these unconventional sources—cleanly, efficiently, and at scale. By isolating lithium directly from water without relying on evaporation ponds or invasive mining operations, DLE opens access to vast untapped U.S. domestic reserves.
While the potential is immense, DLE remains an emerging technology—one that only a few companies globally are starting to prove at commercially viable levels of recovery, purity, and sustainability. DLE technologies that balance performance, sustainability, and cost are likely to define the next generation of critical mineral production. Among the most promising approaches are integrated, modular systems that combine extraction, concentration, and conversion processes into a single platform.
Clayton Valley in Nevada and regions like the Smackover Formation in Arkansas, Louisiana, and Texas, and the Marcellus Shale Formations in Pennsylvania, West Virginia, and New York, are emerging as the proving grounds for this next generation of lithium production. Here, innovative DLE platforms are being piloted in real-world conditions and tested for adaptability to diverse brines and scalability for industrial deployment. As regulatory support grows and urgency around domestic critical minerals intensifies, the outcomes from these early deployments are likely to shape the future blueprint for lithium extraction.
Faster, cleaner, smarter
Compared to conventional methods, DLE slashes production timelines from months—or even years—to just hours or days. It eliminates the need for expansive land use and significantly reduces the environmental footprint. As global demand for lithium surges, DLE represents more than a technical advancement—it’s a radical shift toward cleaner, faster, and smarter mineral production.
DLE also delivers powerful cost advantages over traditional hard rock mining and refining. Its modular, compact design requires far less capital investment, bypassing the need for open-pit mines and evaporation ponds. Operating costs are lower thanks to higher lithium recovery rates—often 60–90% versus 30–50%—and energy-efficient processes that use fewer chemicals. Faster deployment means quicker returns, and it’s a lighter environmental footprint that streamlines permitting and regulatory approval. Combined, these benefits make DLE a breakthrough solution for the next generation of lithium production.
Resilient supply chains start at home
As geopolitical tensions strain access to global mineral reserves, the urgency for domestic solutions has never been greater. DLE offers the U.S. and other hard-rock-constrained nations a pathway to build resilient, local supply chains. This approach opens the door to new jobs and economic activity in otherwise overlooked geographies.
U.S. policy is beginning to catch up. The federal government has designated critical mineral security a national imperative. Programs like the Department of Energy’s MINER initiative are catalyzing research into greener, more efficient extraction methods.
Still, government support alone isn’t enough. It’s time for the private sector to lead.
The call to lead
The minerals needed to power the future aren’t buried in far-off mines in South America and Australia. They’re right here, already flowing beneath us.
Utilities, oilfield operators, and technology innovators already manage the infrastructure, data, and water resources that can power this next frontier. By reimagining wastewater not as a burden but as a resource, we can unlock new revenue streams. In doing so, we also help build resilient domestic supply chains and strengthen national energy security, reducing dependence on foreign lithium sources and securing the materials critical for the clean energy transition.
It’s time to stop digging deeper and start thinking smarter.
Water isn’t just a resource. It’s a solution. For those bold enough to lead, it’s the future.
Prakash Govindan is COO of Gradiant. Anurag Bajpayee is CEO of Gradiant
What's Your Reaction?
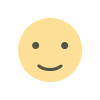
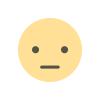
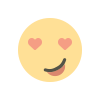
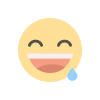
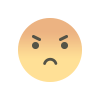
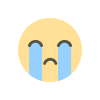
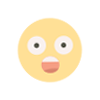