Why James Dyson got into vertical farming
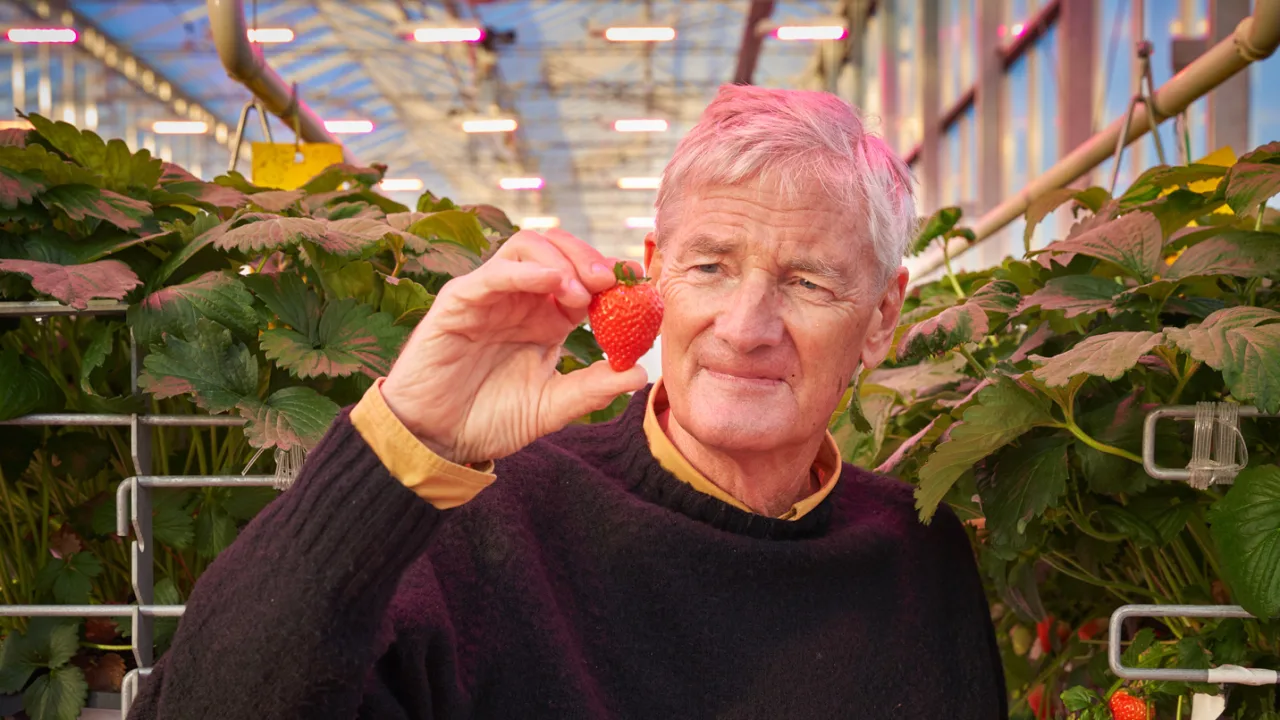
Inside a greenhouse in the English countryside, one of the newest inventions from Dyson just went through its first large-scale test: an 18-foot-tall rotating wheel of strawberry plants, designed to ensure each plant gets its share of sunlight.
Dyson, the multibillion-dollar brand, is best known for designing products like vacuums and ultra-high-end hair dryers. But the company also bought a farm in 2013, and now owns 36,000 acres of land across the U.K.
James Dyson, who grew up in rural England—and hauled potatoes as one of his first jobs—realized that engineering and design could play a role in helping solve some of the challenges of the food system.
“There is a real opportunity for agriculture to drive a revolution in technology, and vice versa,” he says.
Dyson Farming, a subsidiary within the larger family-owned business, is focused on sustainability and food quality. Some of its practices are low tech, such as using crop rotation to improve soil health, or letting wildflowers grow on the edge of fields to support pollinators. But it also continuously incorporates new technologies like sensors and drones.
At a farm in Carrington, England, the company started using an anaerobic digester to turn manure into electricity nearly a decade ago. (The equipment can generate roughly as much power as 10,000 homes use; some of it goes into the grid and the rest is used on the farm.) The process also generates a lot of heat, which is why the farm initially added a greenhouse: The strawberries can make use of the heat to grow in cooler weather. But the team recognized that they could go farther.
“As engineers, we’re never satisfied,” Dyson says. “We constantly ask how things can be improved, achieving better results with the same resources. Instead of relying on traditional rows, we have designed and built a system in which strawberry plants are arranged on rotating wheels which are over 5 meters high, fully utilizing the glasshouse’s vertical space. This dramatically increases the number of plants we can grow in the same footprint, significantly boosting yields by 250%.”
In a typical vertical farm, plants sit on shelves or on walls under artificial light. On the Dyson farm, as the Ferris-wheel-like design rotates, the strawberries get as much access as possible to natural light under the roof of the greenhouse. The farm supplements this with LED bulbs. (A sensor detects the wavelengths of light that the strawberry plants need, and then adds more as necessary.) Making better use of sunlight means that the mechanism also uses less energy.
The system is automated, with robots that use vision sensing to pick berries when they’re perfectly ripe. Other robots distribute predatory insects to fight aphids without insecticide. Another robotic system shines UV light on the berries to prevent mold.
Though the system is still in the early stages, the first crop of strawberries was harvested in May and June, and sold at a premium in U.K. grocery stores because of the quality of the fruit. Eventually, the new tech will be growing strawberries year-round. “Apart from during a few weeks in the summer, the strawberries available in British supermarkets will have been trucked over from North Africa or Spain,” Dyson says. “There is a significant carbon footprint associated with that movement. Plus, the strawberries themselves are small, colorless, and not at all sweet. Our crop is the opposite of that.”
Most of Dyson Farming’s food is still grown outside. But there are advantages to growing indoors when it’s possible, especially as the climate changes. While some other vertical farms have struggled with cost, it’s possible that Dyson’s efficient new invention could help, particularly its model of generating electricity and heat from farm waste on-site. Right now, the biggest cost for vertical farming comes from energy use.
Dyson is interested in scaling up the tech, and potentially sharing it more widely when it’s fully developed. “We are experimenting at this stage, but we’ve unlocked significant efficiency gains for our glasshouse,” he says. “And for others too—while we have to be relentlessly vigilant with confidentiality and secrecy at Dyson due to competitors stealing our innovations, in farming it’s not like that. British farmers have been woefully under-supported by successive governments for years. They need a level playing field with their foreign counterparts. I’m in a fortunate position to be able to take on risk and invest in experimenting with new ways of farming. And I hope it is eventually to the benefit of all farmers. We need to stand together.”
Working on the food system, he says, is not so different from the rest of his life’s work. “Farming shares a lot with engineering and manufacturing,” Dyson says. “You create something, you take pride in it, and you supply it to people who need it. Just as a factory should be efficient, well-designed, and run using the latest technology, the same principles apply to farming. You must get the fundamentals right: drainage, access, boundaries, machinery, buildings, soil health, weed control, and biodiversity. It’s about making everything work together, in the most effective and high-quality way possible. That’s how progress is made.”
What's Your Reaction?
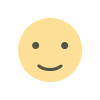
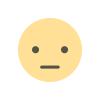
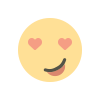
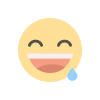
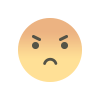
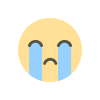
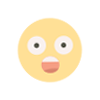