At a new factory in Kentucky, robots will help make your Keen boots
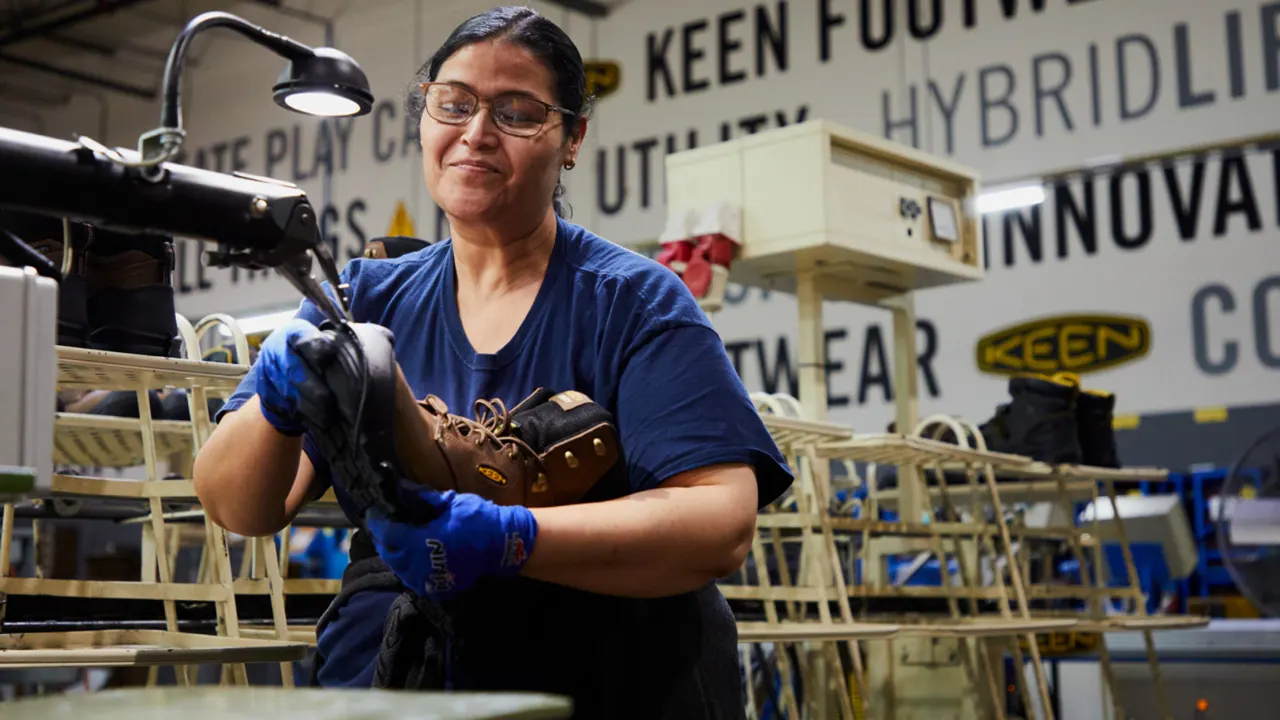
Inside a new factory near Louisville, Kentucky, bright orange robots will soon begin carefully loading boot parts into a machine that adds soles.
It’s one step in the highly automated process of making a Keen work boot—and an illustration of what it looks like now to bring factories back to the United States.
Keen, which is headquartered in Portland, Oregon, started planning the new factory last year, long before current tariffs were in place. And the company, unlike the majority of shoe brands, had already been manufacturing some shoes in Portland for more than a decade.
The Portland factory is now closing as the company prepares to open the larger factory in Kentucky next month. When it first started operations in Oregon in 2010, the business world was skeptical. “Many people told us that [making shoes] could not be done in the U.S., primarily because of some of the cost factors,” says Hari Perumal, Keen’s chief supply chain officer.
The company wanted to be closer to its American market, so it looked for a solution. Labor was the biggest challenge. “Footwear is a very labor-intensive product to make,” Perumal says. And it’s 10 to 12 times more expensive to hire workers in the U.S. than in factories overseas, he says.
The team focused on its high-end work boots, a product with strong demand for an “American built” label. They started by streamlining the process to add soles to the boots. In a traditional factory in Asia, adding soles would happen on a long production line. Instead, Keen turned to a process called direct injection fusing. The shoe’s upper is loaded into a machine where heated polyurethane is molded into an outsole, bonding it directly to the rest of the shoe without glue. Robots also prep materials. In the new Kentucky factory, robots will also handle steps like “flash” trimming of excess material.
Even with advanced automation in place, it’s still more expensive to make shoes in the U.S. than in other countries. Keen plans to continue making many of its shoes elsewhere, including in a factory that the company owns in Thailand. But making boots in the U.S. has some obvious advantages, and the brand plans to continue growing the number of products it makes in Kentucky.
With a U.S. factory, Keen can more nimbly respond to demand from American customers if it needs to make more or less of a particular style. The carbon footprint of delivery is much lower, Perumal says. (Kentucky was chosen strategically since it’s within a two-day drive of 80% of the U.S. population; the company already had a distribution center next door to the new factory.) And customers have made it clear that they want American-made work boots. “We have seen a huge surge in the request for American-built products,” says Perumal.
That’s not to say that the rest of the footwear industry is necessarily likely to follow. Keen struggled to find and keep workers at its Portland factory, despite paying high wages. It also has to invest in training, since American workers no longer have experience making shoes. Because the company has to source components globally—and tariffs now apply to those parts—the cost of manufacturing in the U.S. is now growing even more. The company has pledged not to raise prices for consumers because of tariffs for the rest of the year, however.
To encourage more American shoe manufacturing, Perumal says the government could help by eliminating tariffs on components. “We don’t have a supply chain ecosystem,” he says. “All that’s needed to make the shoes is outside the U.S. right now. It took 40 years to build this global supply chain.”
Even if more factories relocated to America, it’s not clear that there are enough workers who’d take traditional shoe manufacturing jobs. “If you have 4% unemployment in the U.S., are we going to find 20,000 or 40,000 people that want to work for shoe company wages here?” he asks. “Our economy has migrated more toward service.”
The new Kentucky factory will create jobs, but at a small scale: the factory is initially launching with a lean team of 24 skilled production and operations staff. Robots will do the rest.
What's Your Reaction?
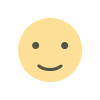
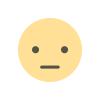
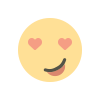
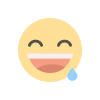
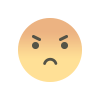
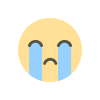
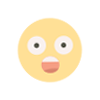