What Is Supply Chain Inventory Control and Its Importance?

Supply chain inventory control is a vital aspect of managing stock levels to meet customer demand efficiently. It involves monitoring inventory to prevent excess stock or stockouts, which can lead to lost sales or increased costs. Effective inventory control relies on accurate demand forecasting and data integration across the supply chain, ensuring that the right products are available when needed. Comprehending its importance can greatly improve operational efficiency and customer satisfaction, but what specific strategies can help you achieve this?
Key Takeaways
- Supply chain inventory control manages stock levels to meet customer demand and optimize operations while reducing costs.
- Accurate demand forecasting is crucial to preventing stockouts and excess inventory, enhancing customer satisfaction.
- Techniques like Just-in-Time (JIT) and Economic Order Quantity (EOQ) minimize holding costs and balance supply and demand.
- Poor inventory control can lead to financial losses due to overstocking or stockouts, impacting overall business performance.
- Implementing technology and advanced analytics improves inventory visibility, accuracy, and responsiveness across the supply chain.
Definition of Supply Chain Inventory Control
Supply chain inventory control is an essential process that involves managing and monitoring stock levels to guarantee you have the right amount of inventory available to meet customer demand.
This method requires tracking product movement, forecasting demand, and integrating data from purchases, reorders, and shipping. By focusing on inventory optimisation, you can improve supply chain inventory optimization, which balances supply and demand as well as minimizing holding costs.
Effective inventory control helps reduce the risk of stockouts, ensuring you don’t face considerable sales losses, like Walmart did in 2014 with $3 billion in losses because of inventory issues.
In the end, a robust inventory control system greatly improves cash flow management by reducing excess inventory, freeing up capital for other crucial business investments.
Significance of Inventory Control in Supply Chain Management
Effective inventory control plays a pivotal role in supply chain management, as it directly impacts product availability and customer satisfaction. When you manage inventory effectively, you can refine operations, reduce costs, and elevate overall business performance.
Poor inventory control, conversely, can lead to financial losses, such as excess carrying costs or lost sales resulting from stockouts.
Consider these key aspects of inventory control:
- Accurate demand forecasting helps you anticipate customer needs.
- Constant inventory monitoring guarantees you maintain ideal stock levels.
- Techniques like Economic Order Quantity (EOQ) and Just-in-Time (JIT) minimize holding costs and improve responsiveness to market fluctuations.
Key Components of Inventory Control
Inventory control encompasses several key components that work together to guarantee smooth operations within the supply chain.
First, planning develops strategies and forecasts demand, helping you set appropriate inventory levels for efficient stock availability.
Next, sourcing identifies suppliers and manages vendor relationships, ensuring you secure necessary materials to support production schedules.
Production oversight includes scheduling and quality control, aligning manufacturing processes with inventory needs.
Furthermore, inventory management supervises stock levels, implements accurate demand forecasting, and manages order quantities to prevent stockouts and overstock situations.
Finally, logistics and transportation monitor the movement of products from suppliers to consumers, playing an essential role in maintaining timely delivery and overall supply chain efficiency, which is critical for meeting customer expectations.
Common Risks and Challenges in Inventory Management
Managing inventory comes with a variety of risks and challenges that can considerably impact a business’s operations. Poor inventory forecasting can lead to waste, especially with time-sensitive products like vaccines. Supplier unreliability may disrupt inventory calculations, affecting stock levels and customer fulfillment.
Furthermore, seasonal demand fluctuations often result in overstocking or understocking, leading to financial losses and inefficiencies.
- High carrying costs from excess inventory can strain resources, complicating profitability.
- A single failure in the supply chain can jeopardize inventory management, highlighting its interconnected nature.
- Accurate demand predictions are vital to minimize waste and guarantee ideal stock levels.
Understanding these challenges is fundamental for effective inventory management in any organization.
Best Practices for Effective Inventory Control
To effectively manage your inventory, accurate demand forecasting is vital, as it helps you predict future needs and minimize stockouts or excess stock.
Organizing your inventory through systems like ABC analysis can improve visibility for high-priority items, making it easier to manage resources efficiently.
Furthermore, constant inventory monitoring through regular audits guarantees your physical stock matches reported levels, enhancing overall accuracy and control.
Accurate Demand Forecasting
Accurate demand forecasting is vital for effective inventory control, as it allows businesses to align their stock levels with actual market needs. By analyzing historical data and market trends, you can predict future inventory requirements, minimizing overstocking and stockouts.
Implementing advanced analytics and AI can improve your forecasting accuracy, identifying patterns in customer behavior. Collaborating with suppliers and stakeholders guarantees timely adjustments based on real-time data.
- Use Demand Supply Integration (DSI) to synchronize supply and demand effectively.
- Apply ABC analysis to categorize products by significance for focused inventory management.
- Regularly review and adjust forecasts according to sales data and market conditions to maintain ideal stock levels.
These practices boost overall supply chain efficiency and help meet customer demand.
Organized Inventory Classification
Organized inventory classification serves as a cornerstone for effective inventory control, allowing businesses to manage their stock with precision.
By implementing systems like ABC analysis, you can categorize products into three tiers—A, B, and C—based on their importance. Tier A items demand the highest visibility and control, guaranteeing you prioritize critical inventory in your management strategies.
This method helps reduce excess stock and minimize carrying costs, ultimately enhancing resource allocation. Furthermore, accurate categorization improves demand forecasting, aligning your supply with customer needs.
Streamlining replenishment processes guarantees that the right products are restocked at the right time, boosting service levels. Overall, organized inventory classification can lead to substantial cost savings and improved cash flow, allowing you to respond swiftly to market changes.
Constant Inventory Monitoring
Though effective inventory control is vital for business success, constant inventory monitoring plays an important role in achieving this objective. By regularly auditing and checking your inventory, you can guarantee that physical stock aligns with reported levels, reducing the risk of stockouts or overstock situations.
Implementing real-time inventory management systems improves accuracy and efficiency, allowing you to track movements instantaneously. Utilize key metrics like inventory turnover ratio and days sales of inventory (DSI) to assess management effectiveness.
- Conduct regular inventory counts to maintain accuracy
- Integrate technology, such as barcode scanning or RFID systems, for real-time tracking
- Monitor key metrics to make data-driven decisions
These practices help minimize carrying costs and boost supply chain responsiveness.
Techniques for Optimizing Inventory Management
Effective inventory management techniques are essential for businesses aiming to enhance their supply chain operations. Implementing Just-in-Time (JIT) can minimize excess stock by producing goods as needed, relying on accurate data. Economic Order Quantity (EOQ) helps determine the ideal order size, balancing holding and ordering costs. Demand Supply Integration (DSI) guarantees your inventory levels align with customer needs, reducing waste. ABC analysis categorizes inventory into three tiers, allowing you to prioritize high-value items. Regular inventory monitoring and cycle counting practices maintain precise stock levels, enhancing efficiency.
Technique | Description |
---|---|
Just-in-Time (JIT) | Produces goods as needed, minimizing excess stock. |
Economic Order Quantity | Balances holding and ordering costs for ideal order size. |
Demand Supply Integration | Aligns supply and demand to reduce waste. |
ABC Analysis | Categorizes inventory to prioritize management efforts. |
Cycle Counting | Maintains precise stock levels through regular checks. |
The Role of Technology in Inventory Control
In today’s fast-paced business environment, technology considerably improves your inventory control processes through AI-driven insights and real-time tracking systems.
By using these advanced tools, you can accurately forecast demand, adjust stock levels quickly, and minimize errors in your inventory management.
This not just enhances your operational efficiency but additionally helps you respond agilely to changes in market demand, ensuring your supply chain remains competitive.
AI-Driven Insights
As businesses face increasing challenges in supply chain management, AI-driven insights are proving essential for effective inventory control. By utilizing real-time data analytics, you can identify trends and enhance stock levels, markedly improving your decision-making processes.
Advanced systems forecast demand more accurately, reducing the risks of overstock and stockouts. Predictive analytics analyze historical sales data, allowing you to anticipate fluctuations in demand and adjust your strategies proactively.
- Automate routine tasks like reorder calculations and inventory monitoring to reduce human error.
- Align inventory levels with actual market needs, improving operational efficiency.
- Maintain ideal stock levels, increasing profitability and reducing carrying costs associated with unsold inventory.
Embracing AI-driven insights can transform your inventory management approach.
Real-Time Tracking Systems
Though many businesses struggle with inventory control, real-time tracking systems offer a strong solution to improve visibility and efficiency across the supply chain.
Utilizing technologies like RFID and barcode scanning, these systems provide immediate insights into inventory levels and locations. You can continuously monitor stock movements, which helps reduce the risk of stockouts and overstock situations.
With real-time data, you can quickly respond to demand fluctuations, ensuring ideal stock levels and enhancing customer satisfaction through timely product availability.
Implementing these systems can lead to significant cost savings by minimizing inventory count errors and streamlining order fulfillment.
Studies indicate that businesses using real-time tracking can reduce inventory carrying costs by up to 30%, improving overall supply chain performance.
Impact of Inventory Management on Customer Satisfaction
Effective inventory management plays a crucial role in enhancing customer satisfaction, especially since timely product delivery is a key factor in retaining customers. When you manage your inventory effectively, you can prevent stockouts that lead to lost sales and frustrated customers.
For instance, 62% of customers stop doing business with a company after poor service related to out-of-stock items.
- Maintaining ideal inventory levels guarantees the right products are available when needed.
- Efficient inventory management reduces excess stock, reallocating resources to improve customer service.
- Transparency in inventory updates cultivates trust and helps manage customer expectations.
Future Trends in Supply Chain Inventory Control
Emerging trends in supply chain inventory control are reshaping how businesses operate, particularly as technology continues to advance. The increasing use of AI and machine learning enables real-time trend analysis, enhancing forecasting accuracy. This helps you respond more effectively to market demand.
Furthermore, the COVID-19 pandemic has accelerated the need for agile practices, requiring advanced inventory management skills to handle disruptions. As e-commerce grows, innovative storage solutions are emerging because of real estate challenges.
Implementing real-time visibility tools and advanced analytics will improve inventory accuracy and reduce carrying costs. In addition, sustainability concerns push organizations to adopt practices that minimize waste, aligning with consumer preferences for environmentally responsible operations.
Adapting to these trends is vital for future success.
Conclusion
In summary, effective supply chain inventory control is essential for aligning stock levels with customer demand, in the end enhancing operational efficiency and satisfaction. By comprehending the significance of inventory management and implementing best practices, you can mitigate risks and optimize your inventory. Leveraging technology further streamlines processes, allowing for accurate demand forecasting and improved cash flow. As trends evolve, staying informed and adaptable will guarantee your inventory management strategy remains effective and responsive to market changes.
Image Via Envato
This article, "What Is Supply Chain Inventory Control and Its Importance?" was first published on Small Business Trends
What's Your Reaction?
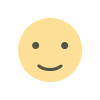
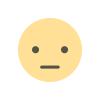
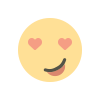
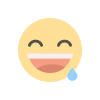
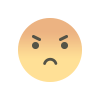
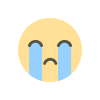
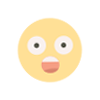