This L.A. startup is using AI and robots to help rebuild faster in the fire zone
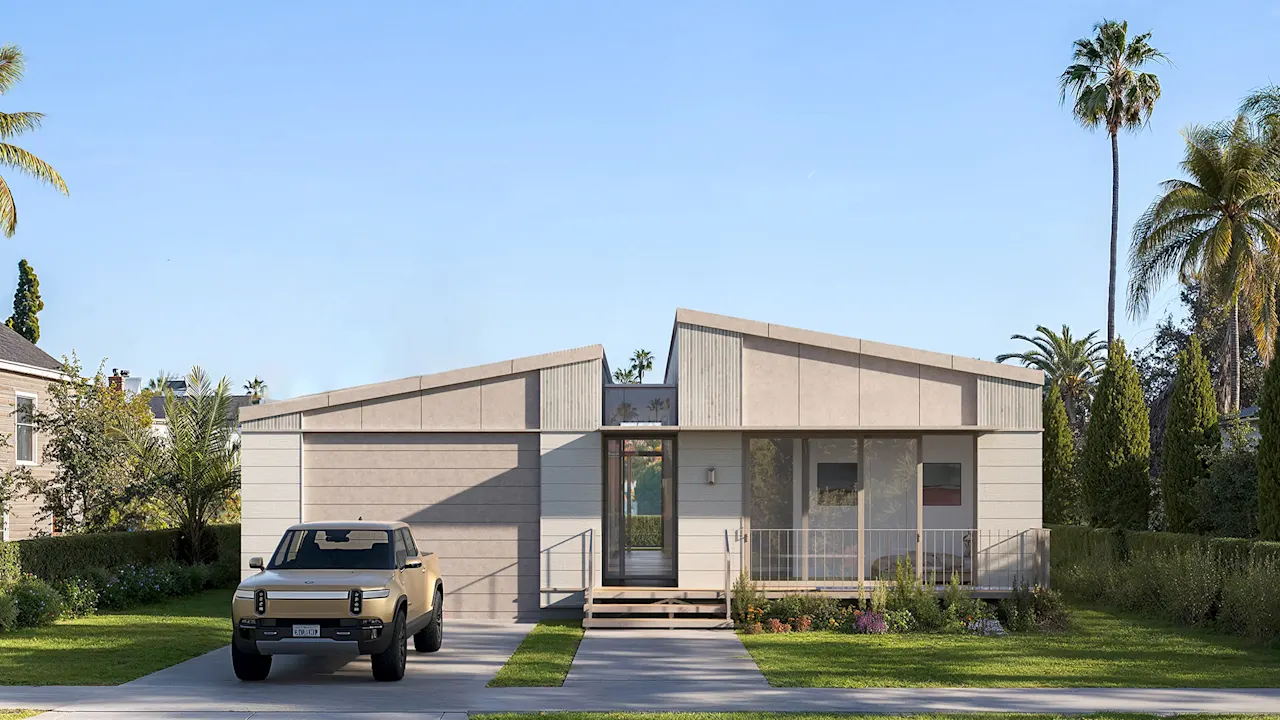
It’s been more than six months since record-breaking wildfires destroyed thousands of homes in the Los Angeles area. So far, few homes have been rebuilt. On one barren block in Altadena filled with vacant lots, no new homes have started construction yet. But one of the first homes that will break ground on the street is using technology to help the rebuilding process move faster.
Later this summer, a mobile “micro factory” will roll up to the lot and begin using robots to build walls, roofs, and flooring panels while a construction crew lays the foundation. Other components, like bathroom “pods” with all of the fixtures preinstalled, will be built off-site and delivered for assembly.
Cosmic, the startup building the house, first launched building sustainable accessory dwelling units (ADUs) with a streamlined process designed to cut time and cost. Last year, the team started designing a larger, fire-resistant single-family home in Northern California. When the disaster hit L.A. in January, the company sped up its work to develop mini factories for the fire zone.
Modular construction isn’t new. But Cosmic’s approach, with compact manufacturing units that travel to the building site, avoids the expense of developing larger factories. (Katerra, one high-profile startup, reportedly spent $150 million on its factory before going out of business.)
“My core belief is that conventional prefab doesn’t work,” says Sasha Jokic, Cosmic’s founder. “We saw the billions of dollars invested in the prefab industry . . . you need to keep the lights on, and it’s super hard to do it, given the costs of operating the factory.” A typical factory is also constrained to a specific geography, since it isn’t economical to deliver more than around 300 miles away.
Instead, Cosmic wants to bring modern manufacturing directly to each site. Its first micro-factory is now sitting on a lot in Pacific Palisades, where the company is working on permits for another house in that fire zone. The factory will travel back and forth between the Palisades and Altadena.
The construction system is around 10 times faster than traditional construction, Jokic says. It also uses around 60% less labor, which may help it avoid disruptions. The construction industry in Southern California already had a labor shortage; the current threat of immigration raids also means that some people now feel afraid to come to work.
The company also uses technology for the design process. For the house in Altadena, for example, it used software to design a house to the clients’ specifications in seven days. “Really, the breakthrough technology is that it’s AI-driven,” Jokic says.
The company, he says, can instantaneously create a code-compliant plan designed specifically for the site and the client’s needs. And because the software will only output designs that the company knows it can build, it’s easy to provide accurate timelines and pricing information.
For families affected by the fires, the company is offering design services for free. The cost of homes is roughly 30% less than traditional construction, Jokic says.
The clarity of the process helped convince the Altadena homeowners to move forward. The family, a couple with a young child, had lived in their previous house—a 1923 craftsman—for a decade. The old house needed repairs, the family had nearly completed a renovation when the fire happened.
After the fire, they wanted to rebuild differently. “We talked to five other architects, and I just felt so overwhelmed by the idea of starting from scratch and going through the rebuilding process again,” says homeowner Justin Lieb. “The renovation was so overwhelming and exhausting.”
They also liked the home’s features, which go beyond the fire safety requirements in the building code, from fire-resistant walls and roofs to sprinklers. The all-electric house is also as energy efficient as possible, so it can make the most of the solar panels on the roof. “Being as self-sufficient and ecologically conscious as possible was a big appeal to us,” Lieb says. A gray water system helps recycle water. They also chose to install an EV charger, though they haven’t yet purchased an electric car.
Software also helped the permit application process go quickly, and the team had filed everything to the city within around 20 days. “As we continue improving the system, really the plan is that this is going to be instantaneous—basically 24 hours turnaround for the concept design, and two days for the permitting,” Jokic says.
The company handles the permitting process. For the Altadena house, it just got approval from the local planning department. Now, it needs approval from the city’s building and safety division, which has committed to a 30-day review timeline. Then construction can begin.
The company is now working through the permitting process for four families in the fire zone. Ultimately, they have the capacity to build as many as 150 to 180 homes over the next 12 months, says Jokic. For every 10 homes they build, they have committed to build another for free for an underinsured family in the fire zone, in a project they call the 1:10 Initiative.
“Given that we can build much faster and lower cost and anyone else on the market, we definitely saw an opportunity for us to donate a portion of our revenue to build for people who [can’t afford it],” Jokic says.
Jokic, who grew up in war-torn Yugoslavia, says that the idea of providing affordable, quality housing has motivated his life’s work. “This is really a deeply personal experience,” he says. “And just being able to help people who are struggling to get their homes back, that’s what really matters at this point.”
What's Your Reaction?
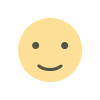
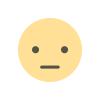
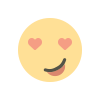
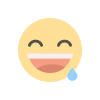
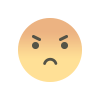
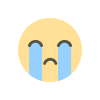
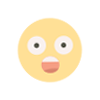